The application of coatings inherently includes personal safety risks. Contractors often encounter jobsites with dusty and/or vaporous conditions, and without proper protection, excessive exposure can result in a number of problems.
Exposure to silica dust, which can occur when construction workers perform many common tasks, has been linked to a heightened risk of silicosis, lung cancer, kidney disease, and other respiratory diseases, according to the U.S. Occupational Safety and Health Administration (OSHA). Meanwhile, the chemicals that comprise coatings, such as common epoxies and resins, could lead to issues such as skin and eye irritation, allergic skin reactions, respiratory tract (nose, throat, and lungs) irritation, allergic respiratory reactions, asthma-like symptoms, or breathing difficulties, according to the U.S. Centers for Disease Control and Prevention (CDC). These problems often occur through inhalation of the coating or if it makes contact with the skin or eyes, and repeated exposure can further add to the risk of injury or illness.
“For contractors, one concern is gases or vapors that are evaporating off the coating,” said Erik W. Johnson, a technical service specialist at 3M, which offers a wide range of personal protective equipment (PPE). “There also could be overspray, if they're spraying. Contractors should always look at the safety data sheet [SDS] to see the chemical makeup and what vapors might be coming off.”
Fortunately, contractors can mitigate many of those hazards through the use of proper safety protocols. The first step is often to try to eliminate the hazard through engineering controls, including the use of dust collection systems, such as vacuums. But if that isn’t enough, choosing the right respirator can be critically important as part of a broader PPE strategy.
OSHA Steps Up Standard
Today, contractors are likely more aware than ever of these concerns following OSHA’s implementation of a stricter standard for crystalline silica. As of Sept. 23, 2017, silica exposure must now be limited to 50 μg/m3 (0.05 mg/m3) as averaged over an eight-hour shift, according to OSHA’s mandate.
“The standard emphasizes engineering controls, primarily,” Johnson said. “Water suppression and dust collectors are the emphasis.”
On some jobs, this might not be enough. And on others where dust isn’t a concern, contractors may still need to be protected from other airborne materials. That’s where respirators could play an even larger role for contractors in the months and years ahead.
“If engineering controls aren’t feasible or if they’re not sufficient, then you may need a respirator to further reduce that exposure,” Johnson said.
Four Steps to Respiratory Protection
Johnson’s company offers a four-point plan to choose the right respirator for a given job:
1. identify the hazard
2. determine the airborne levels
3. determine the level of protection needed
4. choose a respirator
Generally, contractors should protect against particulate hazards — such as dust — with a particle filter, and against gas and vapors with a cartridge. If both types of hazards are present, combination cartridges are an option that can filter out both particles and gas or vapors.
“Step one is identifying the hazards, and step two is learning what the actual airborne levels are,” Johnson said. “It’s not just the percentages listed in the safety data sheet for the material, but it’s what in the air around the workers. They have to do air sampling, and the challenge is whether a contractor has someone on staff that can do that.”
If a contractor lacks an in-house option, Johnson often refers contractors to their insurance carrier, because many times they partner with industrial hygienists. They could also refer crews to consultants affiliated with the American Industrial Hygiene Association (AIHA). Dealing directly with OSHA's consultation services group could also be an option.
“OSHA has a resource group separate from their enforcement group that is designed to help small businesses,” Johnson said. “If they need someone to come out and help with sampling, OSHA may also partner with local universities."
Once collected, the exposure levels can then be compared to the permissible exposure limits (PEL) set by OSHA. If levels are below the PEL, then respirators are not legally required, though they may still want to offer them for optional use. If levels are above the limit and installing suitable engineering or administrative controls is not feasible, then respirators can be used to bring exposures down to an acceptable level.
The third step is to determine the level of protection needed. The only respirators OSHA supports are those approved by the CDC’s National Institute for Occupational Safety and Health (NIOSH). All NIOSH-approved respirators have an assigned protection factor (APF), which can range from 10 to 10,000. To determine what level a jobsite needs, the exposure levels should be divided by the exposure limit. For instance, an APF of 10 means the respirator can protect against exposure levels that are up to 10 times the limit for that hazard. If the exposure level is 500 ppm and the limit is 50 ppm, then an APF of 10 would be sufficient.
That leads into the final step, which is the choice of a respirator type.
“Half-masks are probably the most commonly used respirator [by coatings contractors],” Johnson said. “Whether disposable or reusable, they all have an OSHA assigned protection factor of 10. It doesn't matter who makes it.”
If a higher factor is needed, more protective respirators are available.
“A full-face piece gives you face and eye protection built in, and can have a protection factor of 50 if you do quantitative fit testing," Johnson said. “But it has to be compatible with hard hats, and sometimes fastening the buckle can be problematic.”
A stronger option could be a power-supplied air purifying respirator system (PAPR).
“There’s a battery pack that’s usually on your belt, and air gets sucked through the cartridge or filter and blows the filtered air through a tube that goes up your back and to a head covering that may also serve as a hard hat or welding shield,” Johnson explained. “Even though it’s more expensive and you have to charge the battery every night, it’s an all-in-one solution.”
Importance of Compatibility, Training
Regardless of the choice of respirator, comfort and compatibility with other PPE equipment should be considered. With half-face respirators, glasses could compete for space on the same part of the face — the bridge of the nose — so it’s vital to find equipment that fits together without causing leakage around the respirator edges or a loss of eye protection.
Even after selecting a respirator, understanding how to properly use it on the jobsite is often the final piece to the protection puzzle.
“Those APFs only apply if you follow the whole program,” Johnson said. “Respirators can help reduce exposure, but like with any equipment, it’s all about the training and use patterns. You can’t have it hanging off half of your face, with a full beard, not strapped on, or with cartridges that haven’t been changed. It’s about following the whole respirator training program.”
For contractors, Johnson believes the biggest priority is to fully comprehend the dangers and hazards associated with the job. If they do, it often makes the training process go much more smoothly.
“A lot of the training comes back to whether the workers really understand the hazards they’re working with, so that they’re motivated to correctly wear it all the time,” Johnson said. “If you lift the face piece for even a couple minutes, you’re fully exposed. That can sometimes be all it takes to really hurt you.”
This feature is part of a special anniversary series in 2017 in which CoatingsPro reflects on and updates the magazine’s most-read digital stories. To see the original article from January 2014, please click here. To read the other articles in the Greatest Hits series, click here.
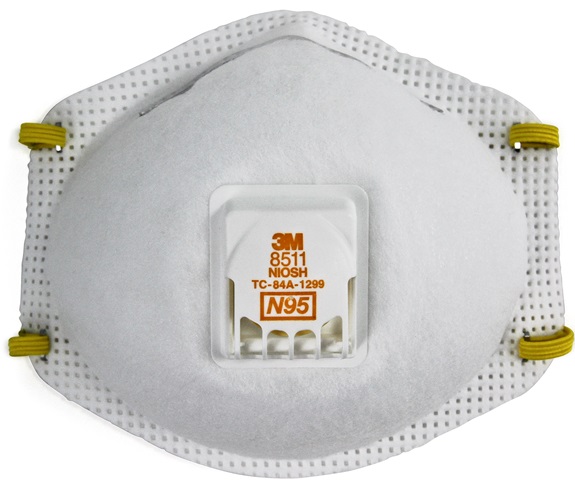